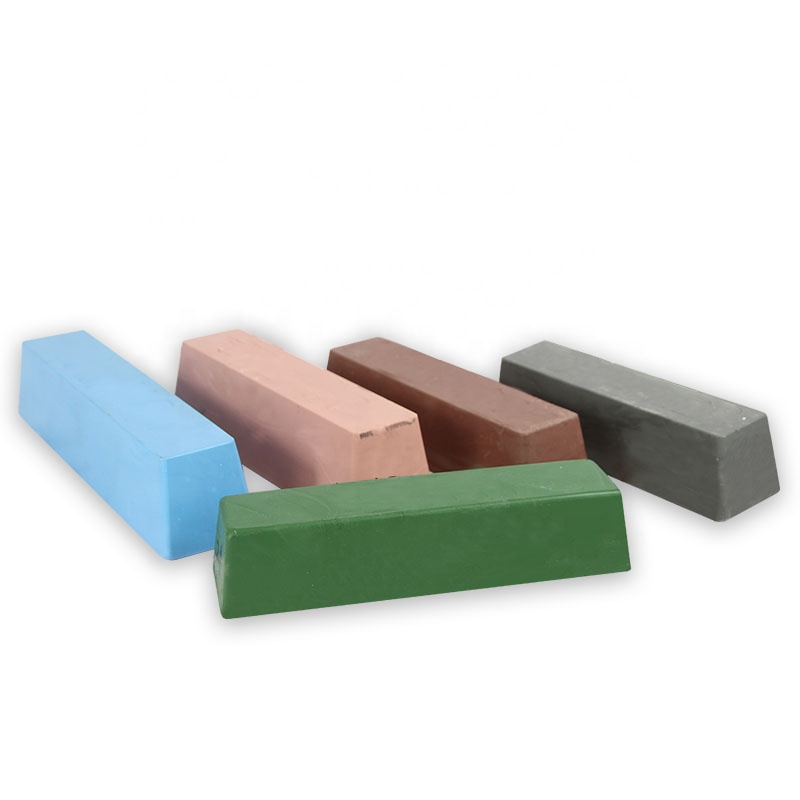
How do you make a polish compound?
Polishing wax/polish compound/polish paste belongs to chemical products and commodities, but in fact it is made by physical mixing and heating. Polishing wax also produces grinding, smoothing, smooth, and bright effects through physical movement during use, thereby playing the role of polishing and polishing. Polishing wax has a wide range of uses. It not only refers to the polishing and polishing of metals, but also the polishing of resins and plastics, as well as hardwood furniture and appliances. At present, the quantity of polishing wax needed in China is huge and there are many kinds. In particular, Guangdong, Zhejiang, Jiangsu and other provinces need more and greater quantities. In addition, there are also a large number of exports to foreign countries.
Polishing compound types
metal polishing wax can be divided into yellow wax series, white wax series, purple wax series (pink), red wax series, green (cyan) wax series, and polishing waxes for special metal products and other materials. . Each series has several varieties or even more than ten varieties, and each variety has its different polishing effect. How to choose a polishing wax suitable for use. According to the requirements of metal material and finish, choose the suitable polishing wax variety.
Polishing wax usage
Polishing, sanding, edging, quilting, polishing, surface treatment before electroplating, polishing, etc. for the surface treatment of various metal products. Polishing is divided into rough polishing, medium polishing, fine polishing and mirror polishing. The polished finish is divided into white light and deep blue light. For metal utensils and utensils of different materials, it is necessary to choose a suitable polishing wax to play a real role and an ideal effect. For example, for the surface treatment of aluminum alloy workpieces and appliances before electroplating, yellow wax is generally used. If there is a higher requirement for the surface of the workpiece, the better yellow wax in the yellow wax series should be used. Purple wax (pink wax) is generally applicable to stainless steel products and utensils. If stainless steel products and utensils are to be scratched and thrown blue at the same time, use purple wax (pink wax), which is better in the purple wax series, and reuse it with higher requirements. Green wax. But this is by no means to say that the same thing is to be done, and the polishing effect required is achieved. In short, it is necessary to decide which polishing wax to use according to the metal material and requirements. The use of polishing wax and the matching of the polishing wheel are also very important. Incorrect matching of the polishing wheel will directly affect the use of the polishing wax.
Composition of raw materials
Metal polishing wax can be basically divided into three types of raw materials, which are formed by heating and mixing grease and abrasive materials, plus additives. In terms of chemistry and chemical engineering, it can be said that it is formed by the heating reaction of base materials and non-base materials and additives.
Raw material selection
The first step in developing polishing wax is to clarify which type of polishing wax should be developed. It is the polishing of aluminum alloy, zinc alloy, copper, iron or stainless steel (tableware, or watchbands, watch cases, glasses frames, and other metal utensils, etc.). Is it soft metal or hard metal. After distinguishing the metal material category, we should also pay attention to the social (market). What kind of grinding power, smoothness and brightness of the polishing wax are required. These requirements must be clarified. When the polishing wax is developed, it will be more direct and faster, and will reduce many detours, which can achieve a half-time effect. Distinguish the type of polishing wax and the required grinding force, smoothness and brightness requirements before selecting materials. While selecting materials, it is necessary to pay attention to the current social (market) sales unit price issues and refer to the products and varieties that can be developed and marketed. Must be when selecting materials.Need to have a certain knowledge and understanding of raw materials.
The effect of grease material on polishing wax
It has good lubricating performance and uniformity for polishing wax and wax body support, and it is a good lubricant, brightener, heat sink and protective agent for metal materials for metals. The melting point is between 48 degrees and 100 degrees, which can meet the requirements that the polishing wax is uniformly mixed in the liquid state under the preparation conditions and is in a solid state at room temperature. It can enhance the oily and delicate feeling, and is a good release agent, paste-forming agent, and brightener. Every kind of grease material has different functions, so when selecting the material, you should choose the one that suits your requirements.
Abrasives materials on polishing wax
The role and use requirements of abrasives on polishing wax: The selection of abrasives should have high hardness and a certain mechanical strength, which is the main component of polishing wax. Abrasives should have the following requirements:
A. The hardness is higher than the hardness of the polished surface metal and good toughness, otherwise it cannot be ground.
B. It has good heat resistance and thermal stability, because during the polishing process, with the high-speed rotation of the polishing wheel, the temperature of the polished surface rises sharply. (The temperature can reach 200 degrees -500 degrees or more) If the abrasive is easy to thermally decompose, its hardness and toughness will decrease, which will affect the polishing effect.
C. It has good stability. The abrasive does not have any chemical reaction with the polished surface at working temperature, otherwise the inherent mechanical properties of the abrasive will change, which will affect the smoothness of the polished surface.
Additives selection
Add a small amount of additives to the polishing wax. After polishing, a protective film can be formed on the metal surface to prevent the metal surface from being polluted by hand sweat and damp oxidation. During the polishing process, the metal surface has a subtle reaction to make the metal The effect of blue light on the surface. Adding an appropriate amount of amine and alcohol substances to the polishing wax can enhance the miscibility of the material, reduce the adhesion of the wax, increase the toughness, and improve the plasticity to ensure the uniformity of the entire wax body. At the same time, the finish of the metal surface can be improved. Add a small amount of spices to the polishing wax to make the polishing wax have a fragrant odor, which can relieve fatigue during work.
Production flow
The production of polishing wax is a physical process in which materials are uniformly mixed. Weigh all kinds of non-moisture materials in proportion. Then put the grease material into the mixing melter to heat and melt, stir evenly, slowly put the abrasive object into the melted grease material mixed melt, and stir to melt it into the oil material paste and mix evenly. Add the additives slowly, stir and mix evenly, heat and stir, (control the temperature of the material in the melter to be between 100 degrees and 180 degrees) and mix evenly until the surface of the wax melt is uniform and shiny. Stop heating and continue stirring to slowly drop the temperature. The temperature drops to below 70 degrees, the wax melt is poured into a pre-prepared mold to cool until the surface of the wax melt is solidified, and then put in cold water to cool and release the mold, and then put in the box for packaging.
CRATOOLS offer the below formula of polish compound, and full set production technology:
- Solid Polish compound in color: Brown,purple,pink, green,white, with different grain size.
- Liquid Polish compound
- Polish Compound solvent
Weclome to inquiry:
Email: [email protected]
Whatsapp/tel: 86-13450474722