Technology for manufacturing bias airway buffing wheels has existed for more than half a century. Over time structural variations of this buff have been developed; some methods more costly than others. Regardless, material still represents a significant portion of this buff’s cost and functionality. Depending on its dimensions and fabric, material can represent between 30 and 85% of an airway buff’s total cost. To understand this more clearly, it is very important to be familiar with the manufacturing process.
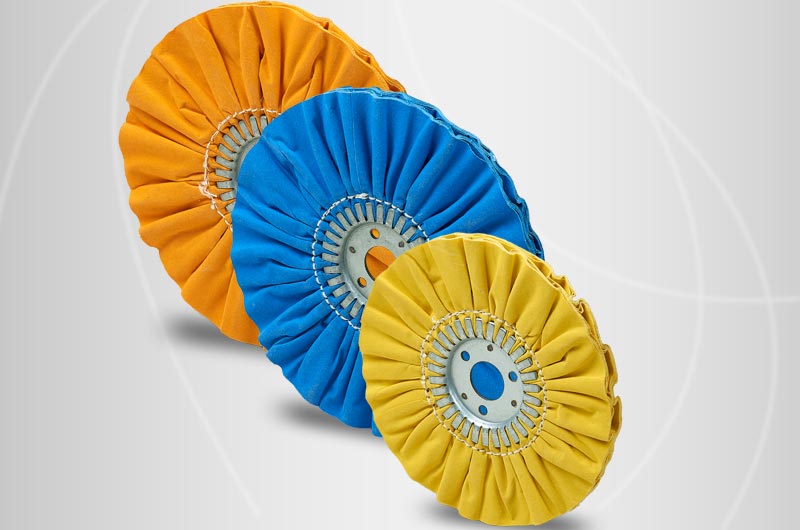
A bias ventilated buff can be made from a number of fabrics. The most common materials are Cotton, Muslin, Flanel and Domet Flannel . The cotton muslin products listed above can be untreated and unbleached. Domet Flannel is napped on both sides and is available bleached and unbleached. A roll of fabric, whether treated or untreated, is bias cut into strips. The ends of the strips are sewn together into a continuous roll. The resulting roll is trimmed to the proper length and width for the next process.
The Iris is named for the motion of the blades. This motion is similar to a camera shutter. As the inside diameter or aperture of the blades decreases, the material around the drum is folded in half and evenly pushed into the center channel. The teeth of the clinch ring are pressed into the fabric. The resulting buff has a pleated or “puckered” face.
At the “Iris” machine, biased material is wrapped around a large round drum (also called a mandrel, hub or core). The drum size depends upon the desired dimensions and amount of cloth in the buff. Circularly converging steel blades force the fabric into a steel clinch ring in the drum’s center channel.
By using biased fabircs in this configuration, all thread ends are exposed to the buffing surface at a 45 degree angle forming a “V”. Each thread runs from the periphery of the buff through the clinch ring and back out to the periphery on the other side. This enhances the structural integrity of the wheel while also minimizing fraying and raveling.
The pleats allow airflow through the buff, which cools it and the part surface. The pleats also stiffen the wheel, enhancing cutting capabilities. Additionally, pleating engenders greater compound adherence. The amount of pleating in a buff is dependent upon the yardage in each ply of cloth. Ply refers to the number of fabric layers in the buff’s face. Since the Iris’s blades fold the material in half, eight layers of drum wrapped fabric are needed to make a 16-ply buff. The more material in the buff, the greater the pleating. A buff’s density, pleating number, pack and class number denote the amount of pleating or cloth per ply. Assume you are wrapping material around an Iris machine’s drum in order to make a 16-inch outside diameter, seven-inch inside diameter, 16-ply buff. If an 18-inch drum is used, the density of the buff is two (18-inch drum size minus 16-inch outside diameter equals two). If a 20-inch drum is used, the density or pack is four.
By using a larger drum, more biased material is added to each ply of the buff. In the above example, a No. 4 density buff would have more than six linear inches of biased material per drum revolution than a No. 2 density buff. (20 x 3.1416 [p, Pi] = 62.83 linear inches; 18 x 3.1416 = 56.55 linear inches; 62.83 – 56.55 = 6.28 linear inches more material.) In total, this No. 4 density buff has 11 pct more material than the same size No. 2 density buff. The corresponding price differential should also be between nine and 11 pct. Depending on the application, the increased production life of the No. 4 buff may make it worth the added expense. Conversely, buying a buff with more density than required is an obvious waste of money. Thus, matching the right density to the application is critical.
To measure the density of an existing buff, cut one strip of cloth from the buff’s first ply or layer. Make sure to cut one complete revolution around the clinch ring. It does not matter how wide the strip is. Next, lay the strip out flat and measure its length. Divide the strip length by 3.1416 (p). The resulting number should estimate the drum size used to manufacture the buff. Subtract the buff’s original outside diameter from this estimated drum size to derive the density; i.e., No. 2, No. 4, No. 6. By calculating the density and performing some time studies with various alternatives, you can determine which density or combination of densities maximize productivity.
Because of increasing cost-reduction pressures in automatic and semi-automatic operations, there has been a tendency to equate increased efficiency with a lower buff price rather than a lower cost per finished part. Some companies are experimenting with smaller wheel diameters or fewer plies of fabric per buff in order to reduce costs. Unfortunately, many find that instead of reducing costs they spend more on the overall buffing operation due to more frequent buff changeovers, reduced finishing capabilities that cause longer dwell times and more rework.
Buffing is a chemical and mechanical action. Regardless of the cloth used, cotton, sisal, wool, polyester/cotton blends, a buffing wheel acts primarily as a carrier of abrasive compound to the part’s surface. Thus, for developments to be beneficial, they must enhance the buff’s carrying capability or increase the time that compound can effectively be carried. A truly improved buff must cut and/or color faster for longer periods achieving the same or better (consistent) results for less money per finished piece. Therefore, arbitrarily reducing fabric content to lower costs may be self-defeating.